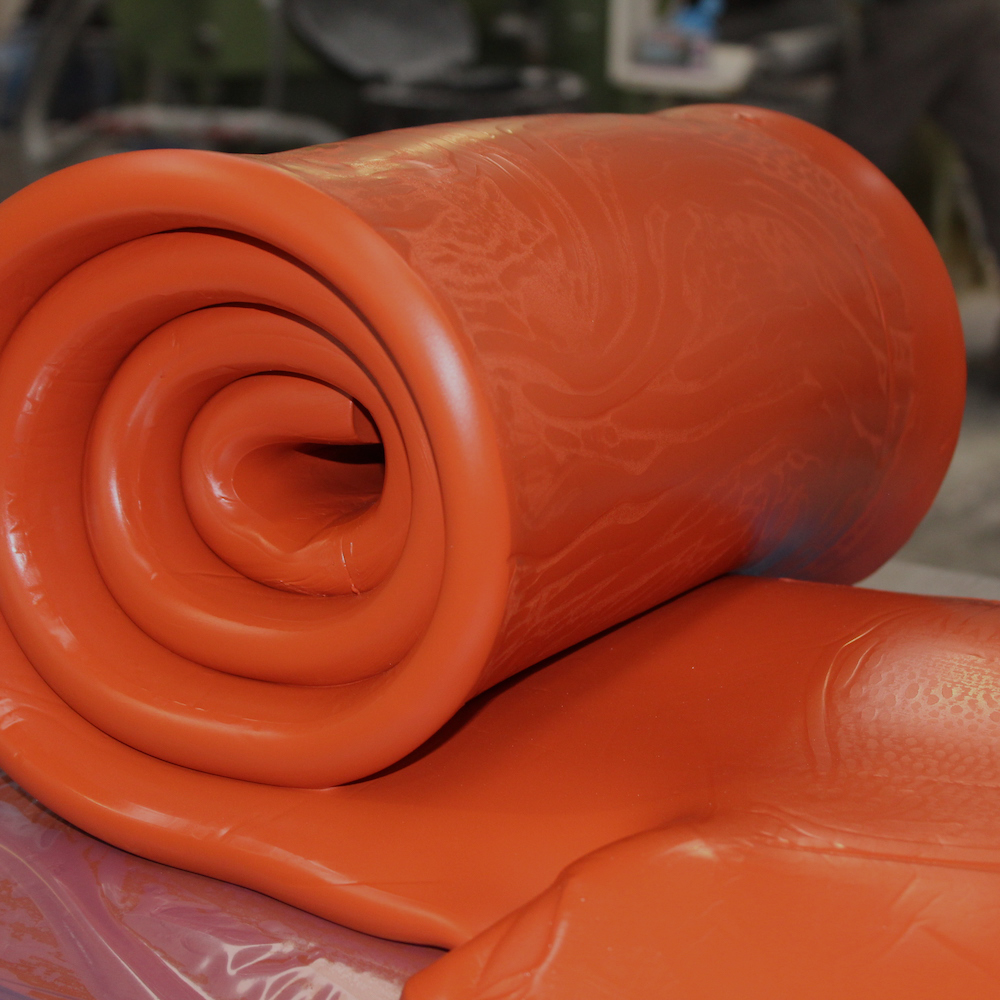
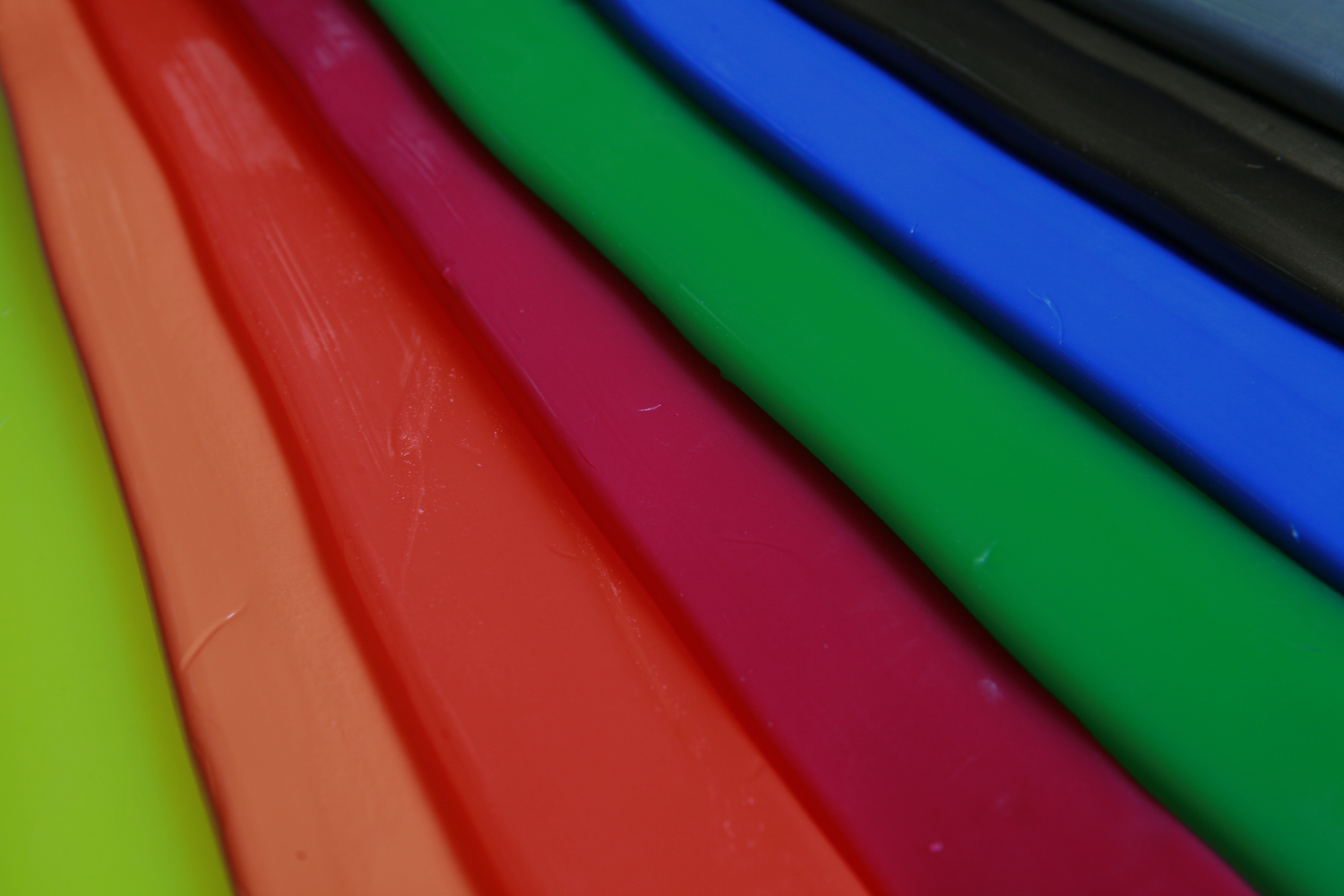
Silicone rubber compounds
Description
Silicone rubber (VMQ and FVMQ) is a highly versatile elastomer that can be used in many diverse sectors. Industrial grades of silicone rubber are generally based on polydimethylsiloxanes, partially substituted with other organic groups such as alkyl, vinyl or phenyl, which regulate respectively the processability, reticulation and resistance to low temperatures. In the special case of fluoro-silicone rubber, one of the two methyl groups is substituted by a trifluoropropyl group. This unique feature results in a better resistance to fuels, solvents and to non-polar oils, as well as in an improvement of the compound performance at low temperatures. The incorporation of reinforcing fillers – typically precipitated or amorphous-ventilated silica – yields the formulations the hardness and the mechanical properties suitable for a static or dynamic application.
Thanks to a unique combination of chemical-physical properties, silicone rubber compounds possess remarkable characteristics:
- A wide temperature application depending on the grade from -150°C to +250°C with peaks up to +300°C
- Flexibility, resilience and steady sealing properties at a wide range of temperatures
- Excellent resistant to atmospheric agents such as rain, snow, humidity, sunlight und UV light
- Long-lasting and excellent insulating properties
- Natural resistance to fire and toxic-free combustion products
- Wide hardness range (from 10 to 90 ShA)
- Easy to colour (from transparent to opaque and from fluorescent to textured or glittered)
- Chemical and biochemical inertia
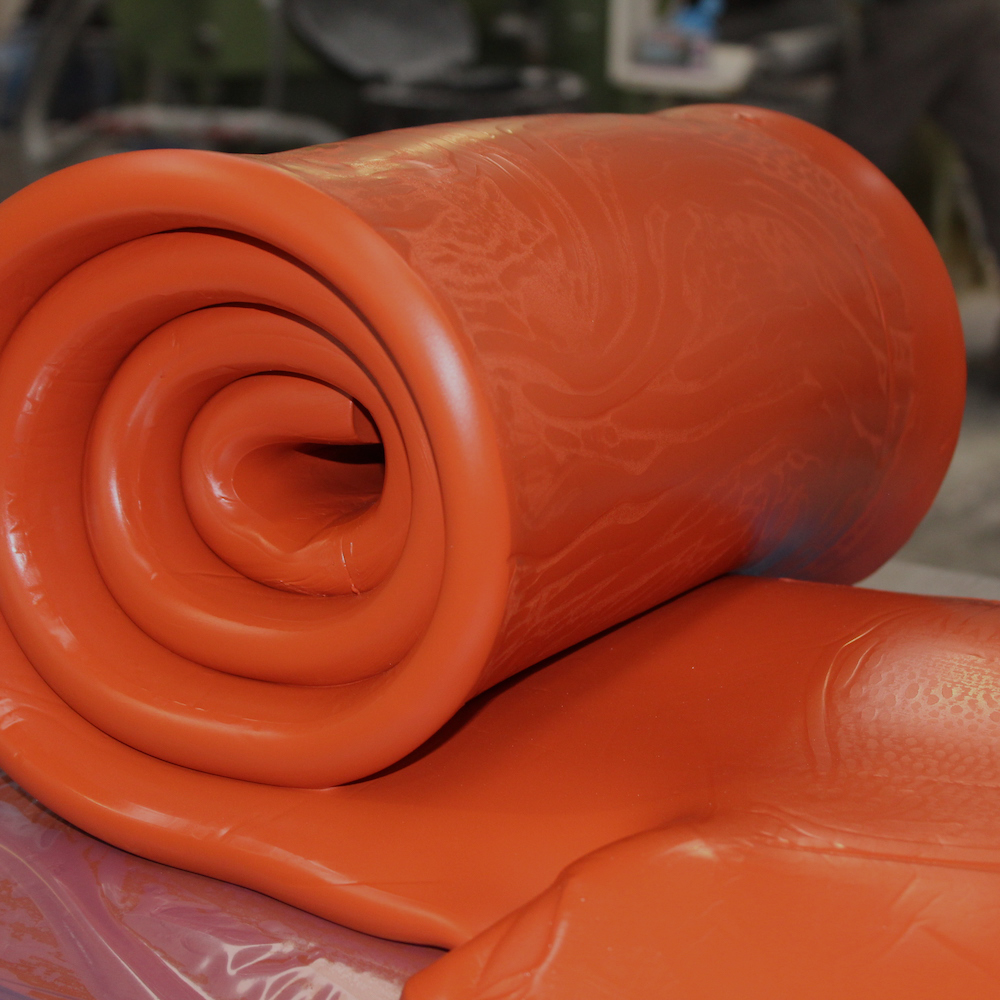
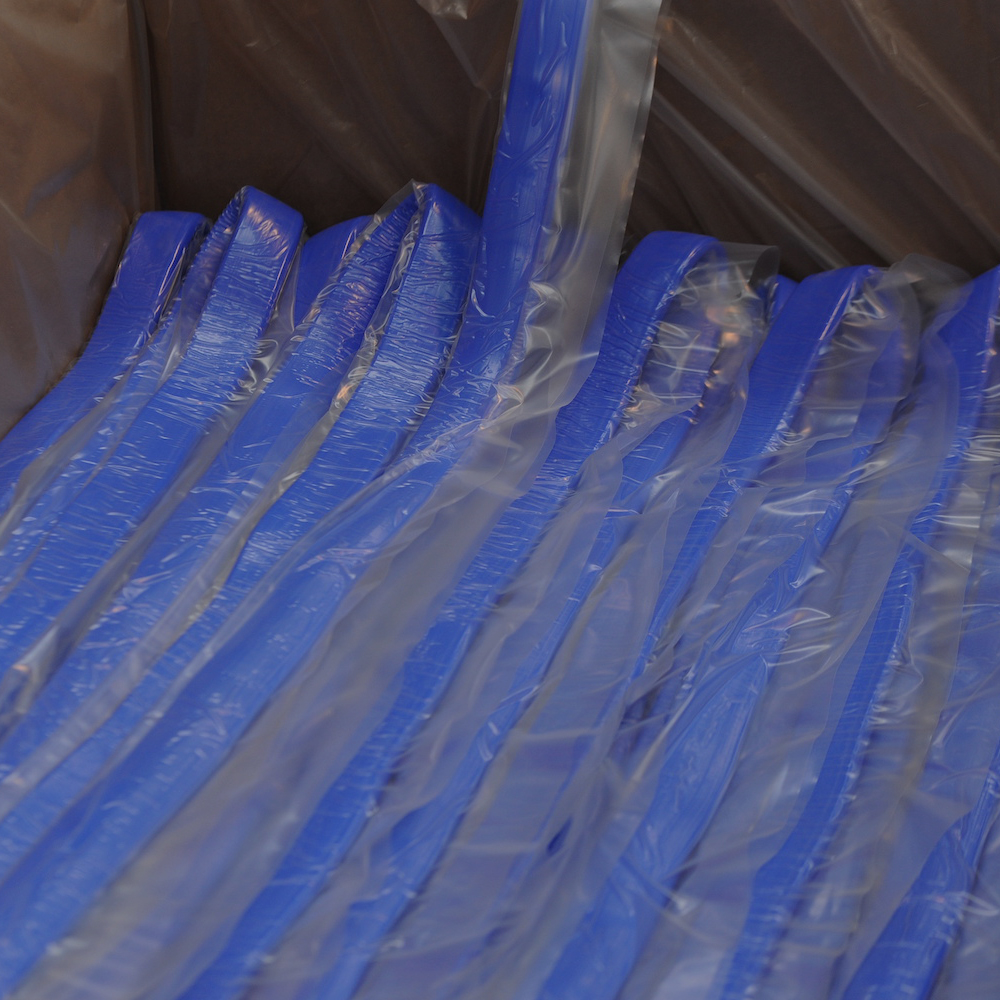
Processing
Silicone rubber compounds are also versatile when considering the transformation possible per extrusion and reticulation (in hot air, microwave, salt bath and steam), calendering or coating, per compression or injection moulding. Silicone rubber compounds reticulation can occur via radical reticulation by using peroxides or via catalyst reticulation by using organometallic complex of platinum. In particular, this second type of reticulation yields odourless and flavourless articles suitable for contact with potable water, food or for the manufacturing of medical appliances.
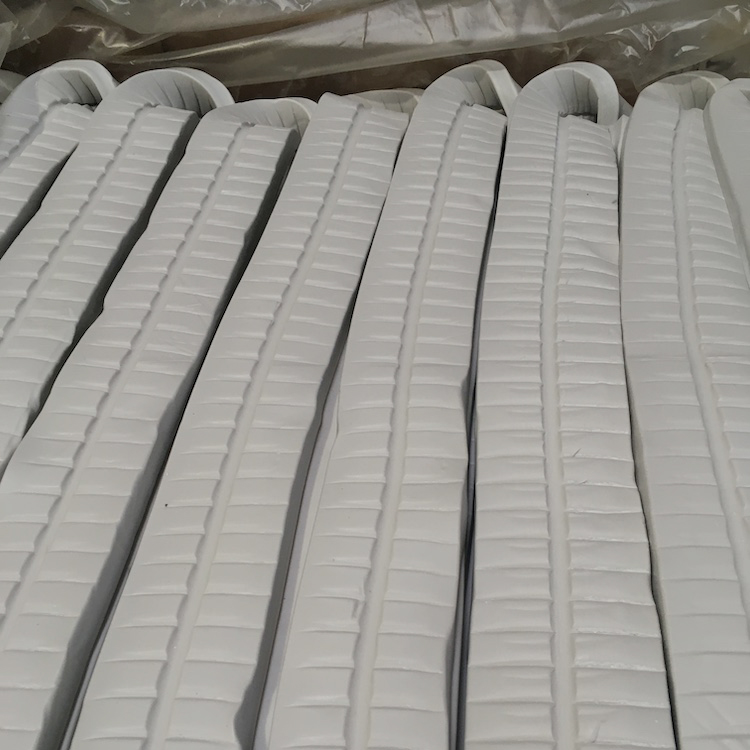
Processing
Silicone rubber compounds are also versatile when considering the transformation possible per extrusion and reticulation (in hot air, microwave, salt bath and steam), calendering or coating, per compression or injection moulding. Silicone rubber compounds reticulation can occur via radical reticulation by using peroxides or via catalyst reticulation by using organometallic complex of platinum. In particular, this second type of reticulation yields odourless and flavourless articles suitable for contact with potable water, food or for the manufacturing of medical appliances.
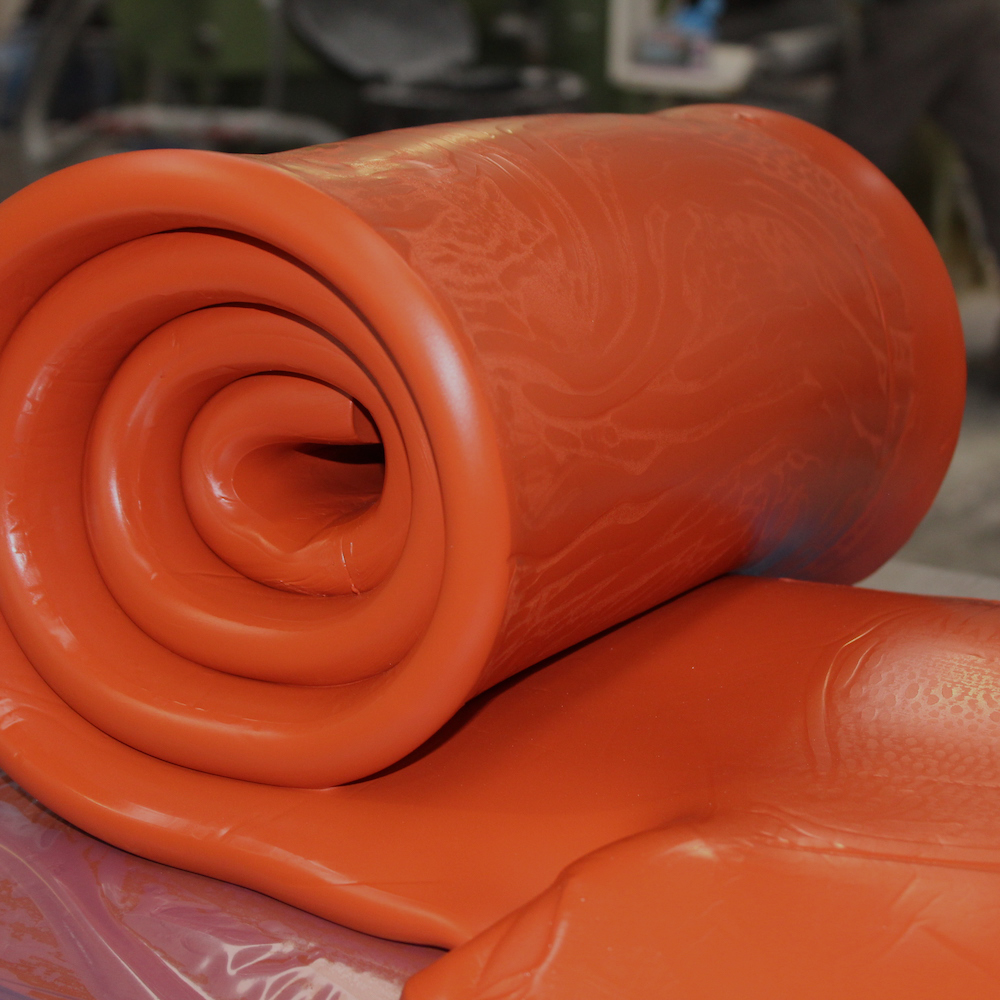
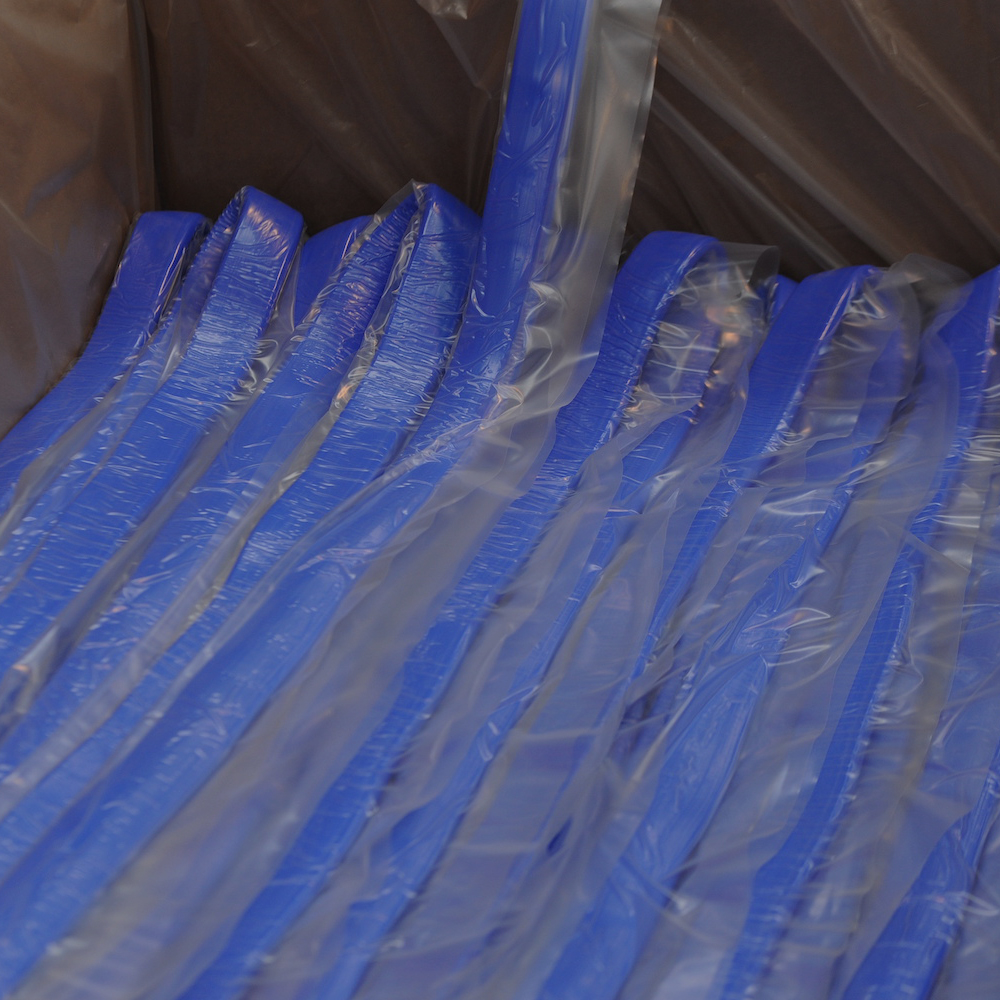
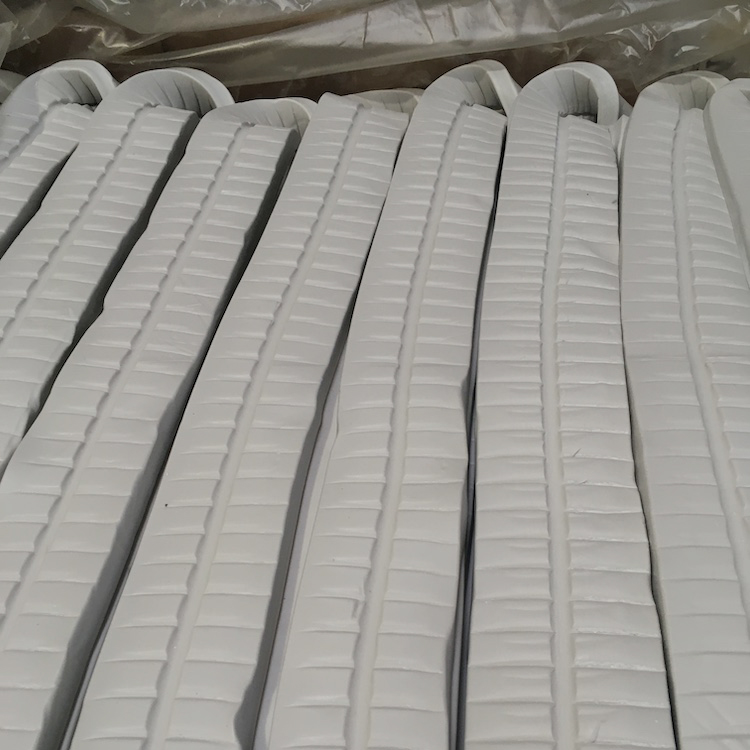
Market segment
- Automotive
- Transportation
- Industrial
- Oil & gas
- Agriculture
- Energy – W&C
- Building & construction
- Printing and labelling
- Houehold appliances
- Consumer goods
- Food & beverage
- Sport and leasure
Packages
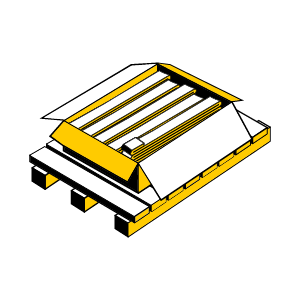
Width | from 35 mm to 90 mm |
Thickness | from 10 mm to 20 mm |
*possibility to filter
*possibility of customization
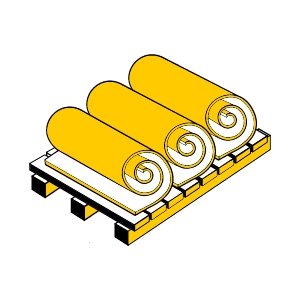
Width | 400 mm |
Thickness | from 10 to 20 mm |
*possibility of customization
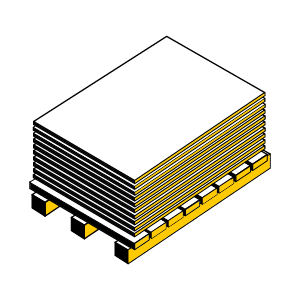
Width | 400 mm |
Thickness | 20 mm (± 20 mm) |
Length | 1200 mm |
*possibility of customization
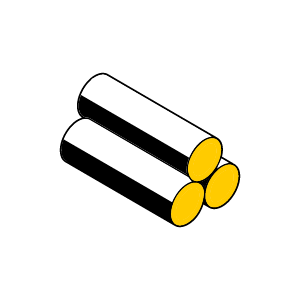
Diameter | from 60 mm to 150 mm |
Length | as required |
*possibility of customization
*possibility to filter
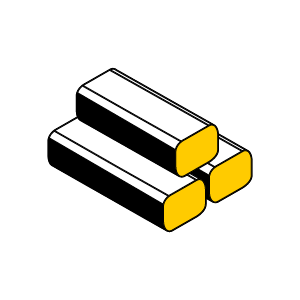
Diameter | from 60 mm to 150 mm |
Length | as required |
*possibility of customization
*possibility to filter
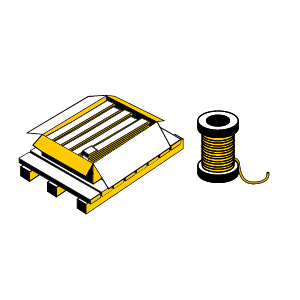
This solution allows to make direct colouring of a natural compound in extrusion. The special packaging allows to introduce the colour rope in the extruder combined with a silicone rubber compound natural stripe. |