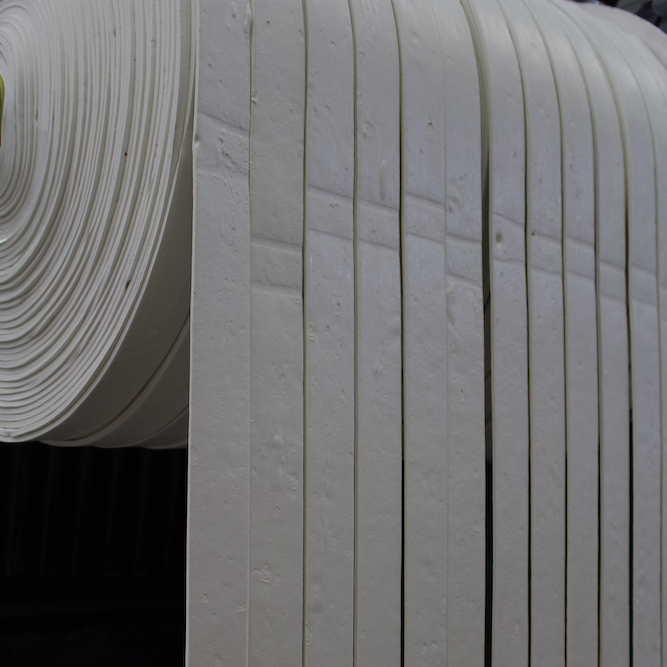
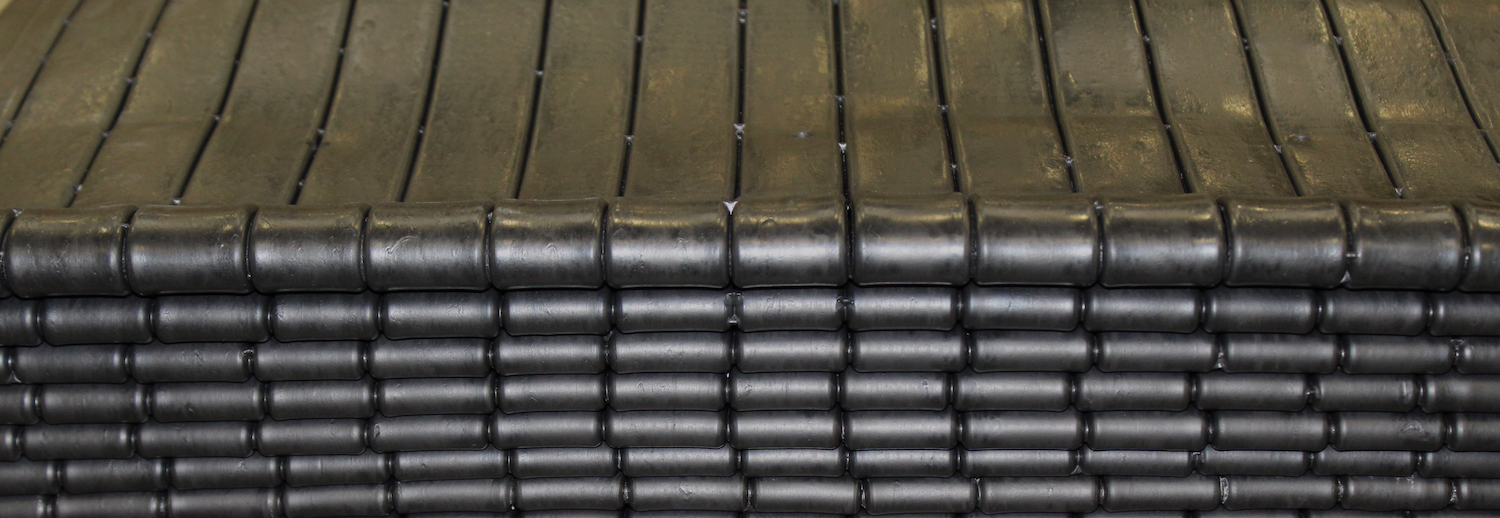
Synthetic and natural rubber compounds
Description
Organic rubber family includes a wide variety of elastomer materials. Polymers adopted in organic rubber compounds can be the simple plain rubber tree coagulated latex or the enormous variety of products developed over the years by the petrochemical industry such as EPM, EPDM, NBR, SBR and CR among the most common grades, HNBR, ACM, EU, AU, ECO, CSM etc. There are 30 existing classes of organic elastomers, each of them found on the market in many diverse grades. The combination of reinforcing or non-reinforcing fillers, activators, cross-linkers and plasticisers may result in endless ingredients combinations for endless applications: static or dynamic, in contact with the most different fluids and at the most diverse temperature and climate conditions.
Each organic compound type possesses precise properties and exceeds in one or more aspects, such as:
- Synthetic (IR) and natural polyisoprene (NR) rubber: excellent mechanical properties, ideal for dynamic employments
- Acrylonitrile butadiene (NBR) and (partially) hydrogenate acrylonitrile butadiene (HNBR) rubber: high resistance to oils, hydrocarbons and gases
- Butyl rubber (IIR): low gas permeability
- Ethylene-propylene copolymer (EPM) and ethylene-propylene-diene terpolymers (EPDM): excellent resistance properties to weathering and flexibility at low temperatures
- Chloroprene rubber (CR): excellent balance between mechanical properties and chemical resistance to weather conditions
- Acrylic acid (ACM) and ethylene acrylic ester copolymer (AEM): excellent high temperature and lubricants resistance
- Polyurethane polyether (EU, AU): the highest resistance to abrasion
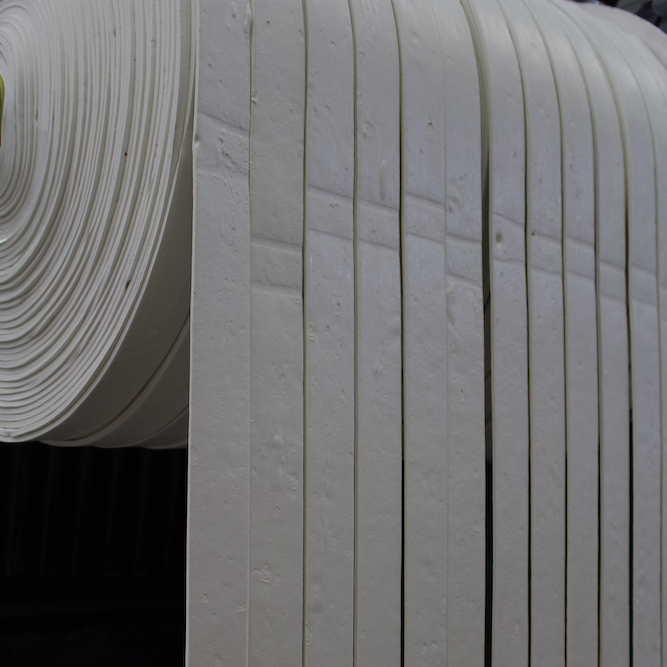
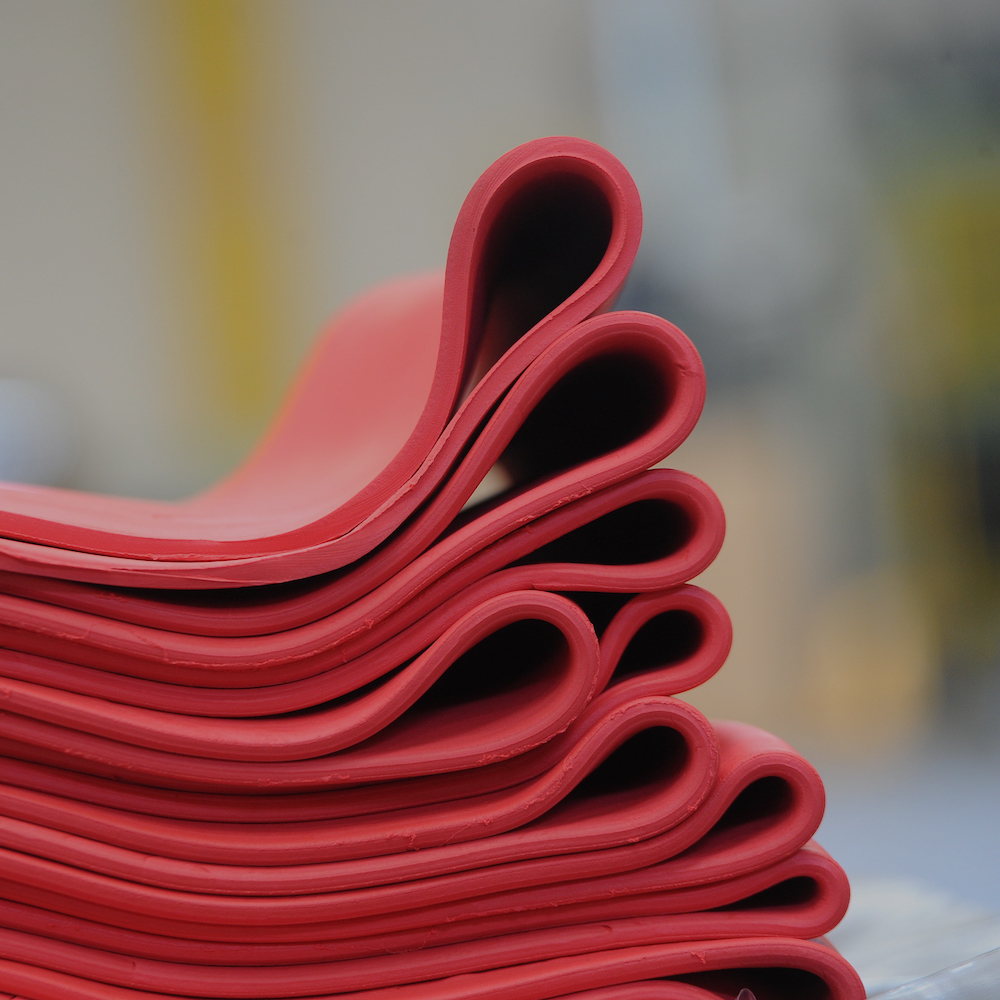
Processing
The manufacturing technologies of these types of compounds are the traditional compression and injection moulding, extrusion, calendering and coating process. All unsaturated elastomers are generally reticulated through sulphur, but peroxides can also be used. Those which do not have unsaturated bonds like EPM compounds can be reticulated with peroxides only. Some specialities require exclusive reticulation agents that take advantage of specific chemical properties.
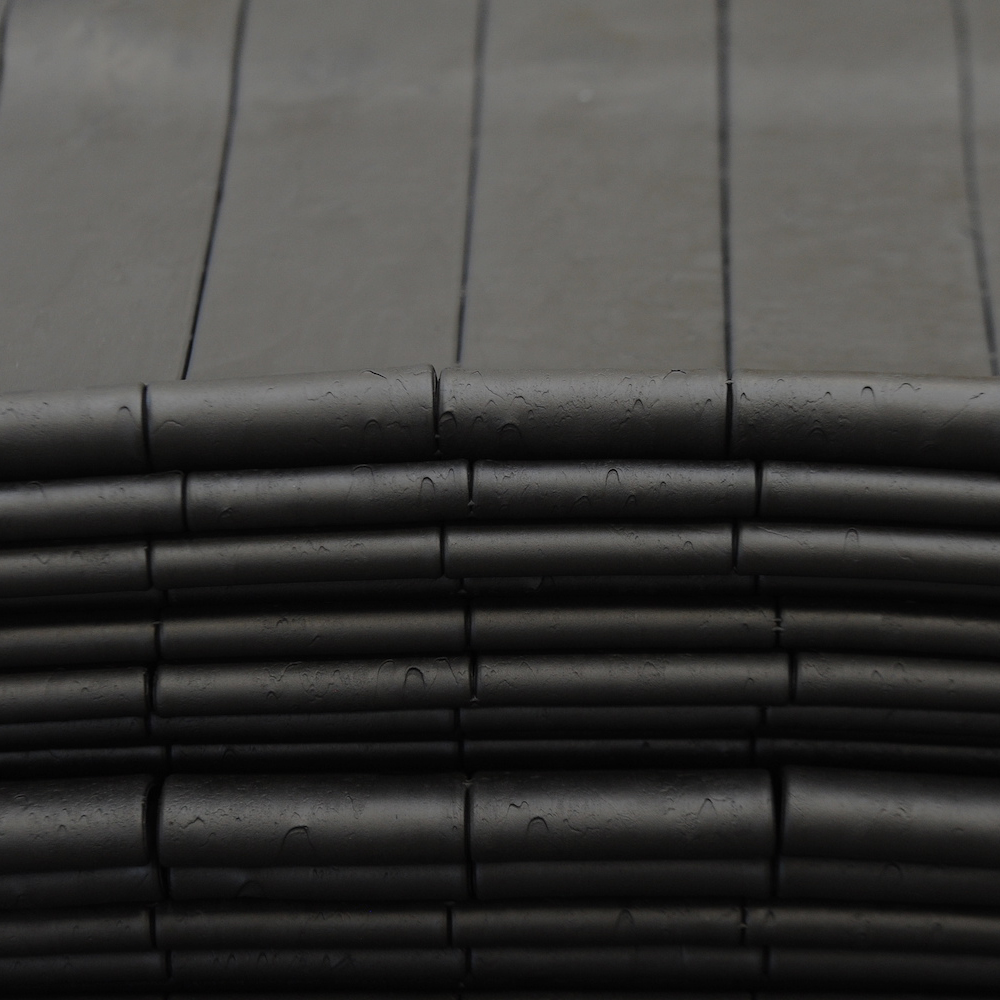
Processing
The manufacturing technologies of these types of compounds are the traditional compression and injection moulding, extrusion, calendering and coating process. All unsaturated elastomers are generally reticulated through sulphur, but peroxides can also be used. Those which do not have unsaturated bonds like EPM compounds can be reticulated with peroxides only. Some specialities require exclusive reticulation agents that take advantage of specific chemical properties.
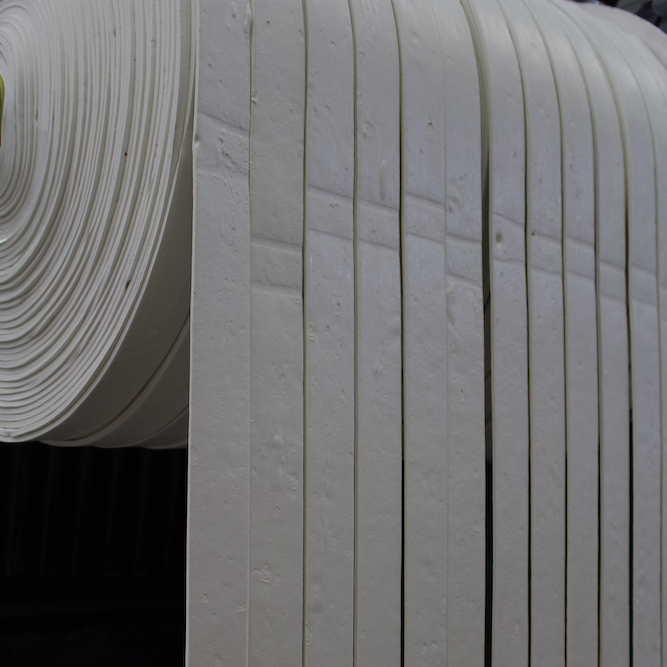
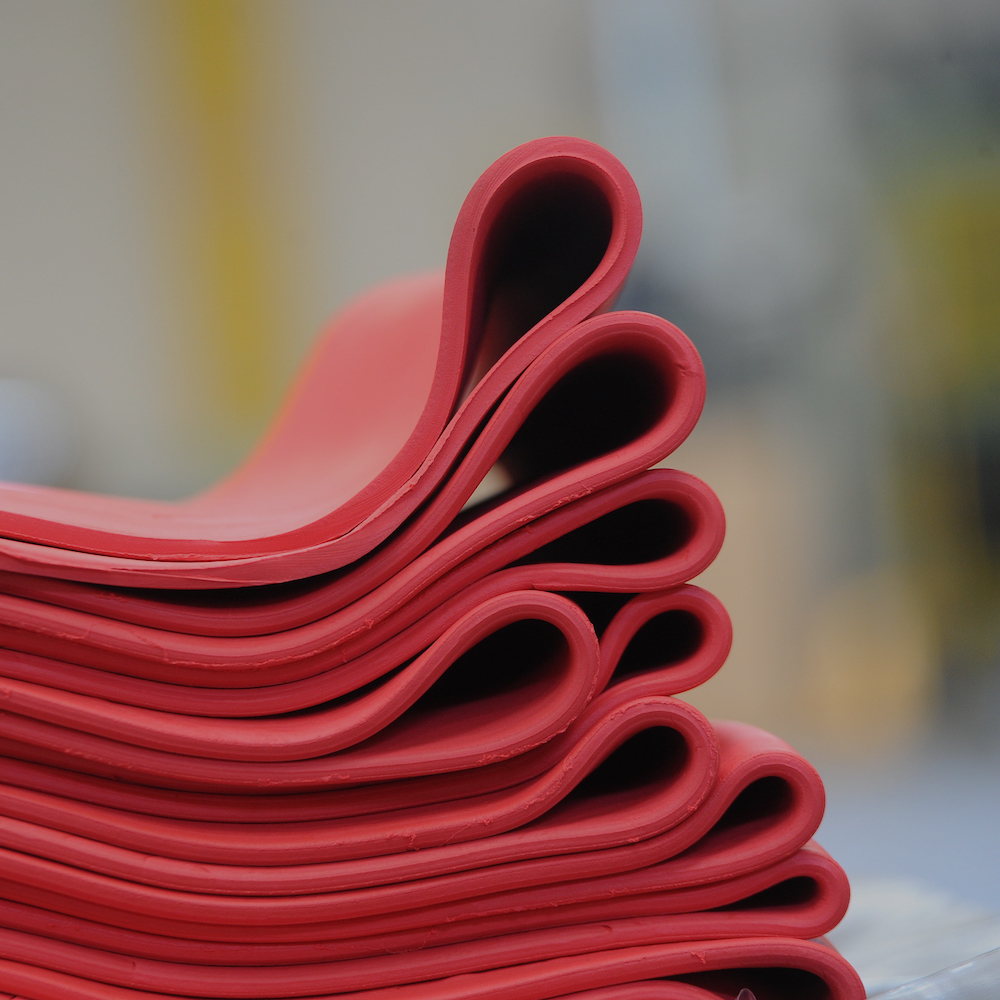
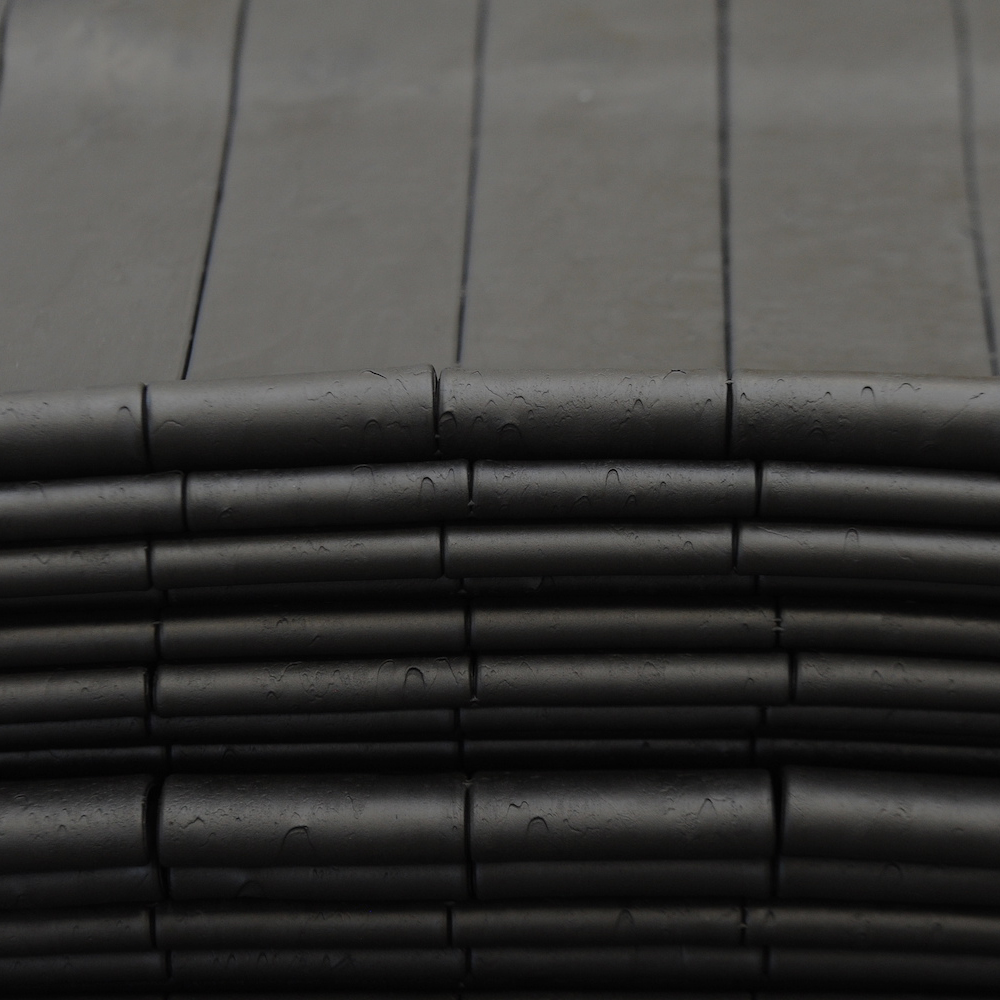
Market segment
- Automotive
- Transportation
- Industrial
- Oil & gas
- Agriculture
- Energy
- Buildin & construction
- Printing and labelling
- Houehold appliances
- Consumer goods
- Food & beverage
- Sport and leasure
Packaging
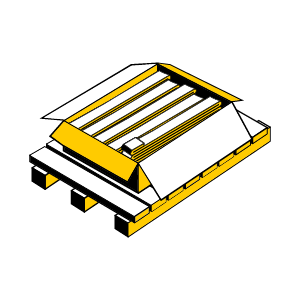
Thickness | from 5 mm to 12 mm |
*possibility of filtration
*possibility of customization of width (from 25 mm to 100 mm)
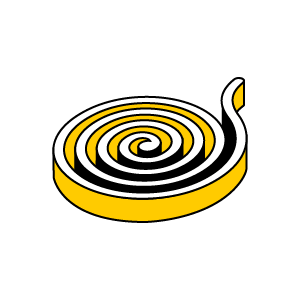
Width | 40 mm (± 5 mm) |
Thickness | 8 mm (± 3 mm) |
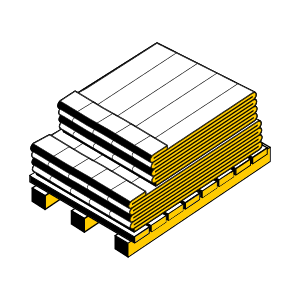
Width | 40 mm |
80 mm (± 5 mm) | |
120 mm (± 5 mm) | |
360 mm (± 5 mm) | |
Thickness | 8 mm (± 3 mm) |
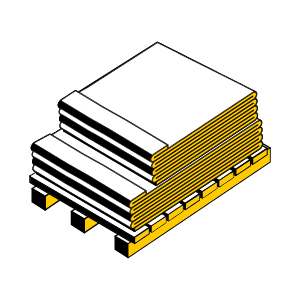
Width | 500 mm (± 100 mm) |
Thickness | 8 mm (± 3 mm) |
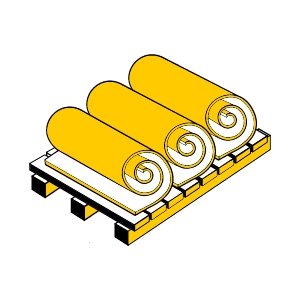
Width | 500 mm (± 100 mm) |
Thickness | 8 mm (± 3 mm) |
Max weight | 25 kg |
*possibility of customization
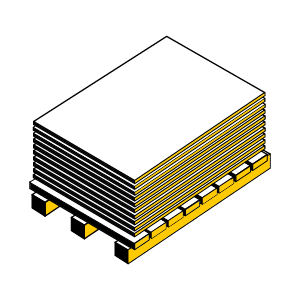
Width | 500 mm (± 100 mm) |
Thickness | 8 mm (± 3 mm) |
Length | 1000 mm (± 200 mm) |
*slabs without anti-tack
*possibility to add polyethylene
*possibility of customization